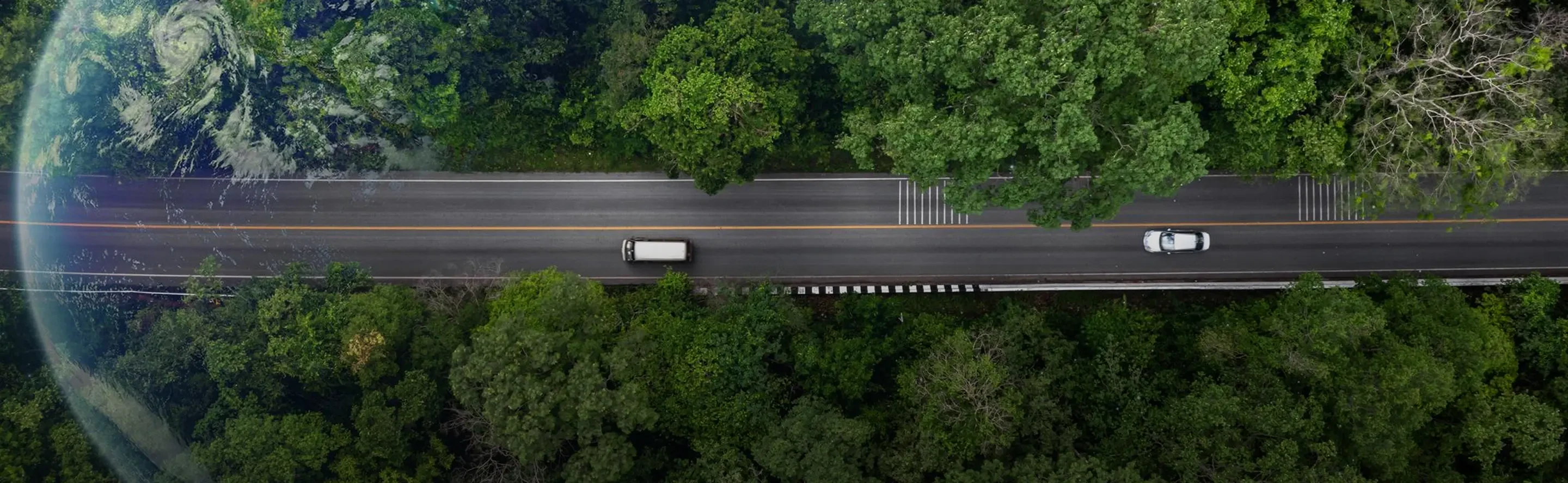
Supply Chain Management
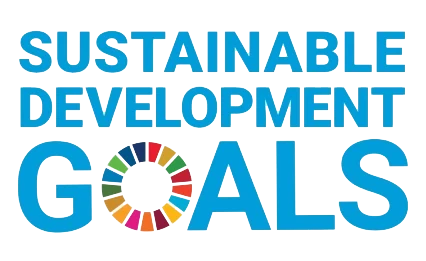
Importance and Mission
Ichitan Group Public Company Limited is committed to managing the supply chain responsibly and adhering to the Supplier and Business Partner Code of Conduct, which covers everything from supplier selection, procurement, assessment, audit, monitoring and promoting suppliers to comply with the Sustainable Procurement Policy. In addition, the Company has screened and assessed all suppliers using ESG criteria to align with the Company’s sustainable development approach, and reduce risks that may impact environment, human rights and business ethics, to create transparency and accountability throughout the supply chain. The Company has managed the sustainable supply chain by building a network of cooperation with all sectors to achieve long-term goals together in line with the United Nations Sustainable Development Goal (UN SDGs) No. 12 on promoting sustainable procurement practice.
Stakeholders Directly Impacted
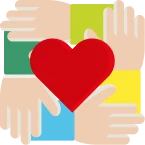
Society and Community
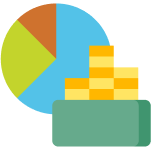
Business Partners / Creditors
Goal and Performance Highlights
Goals
Performance Highlights
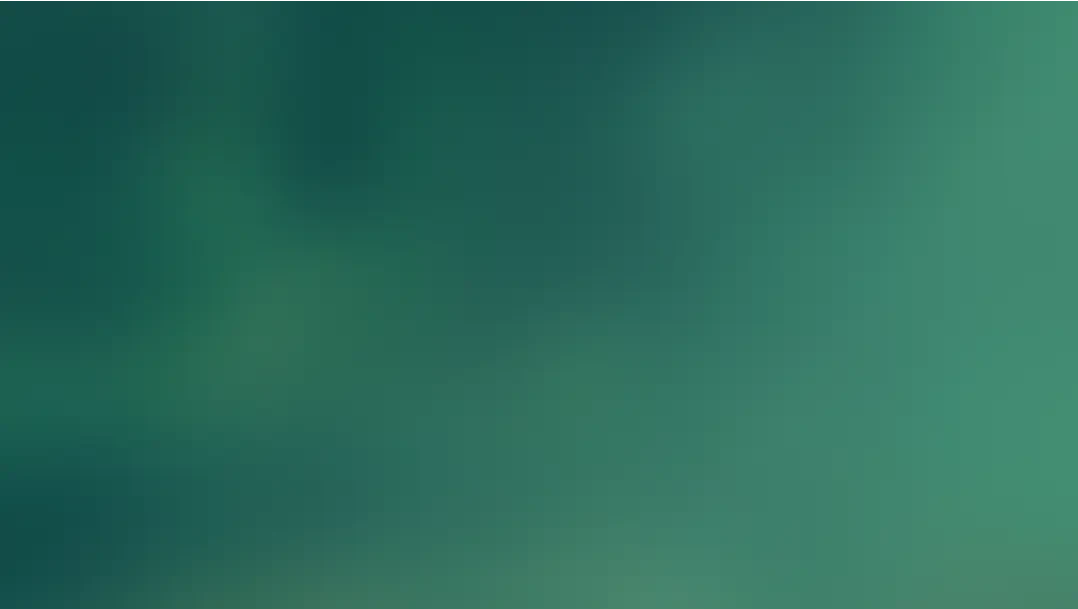
of suppliers were communicated about
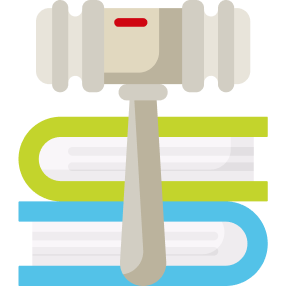
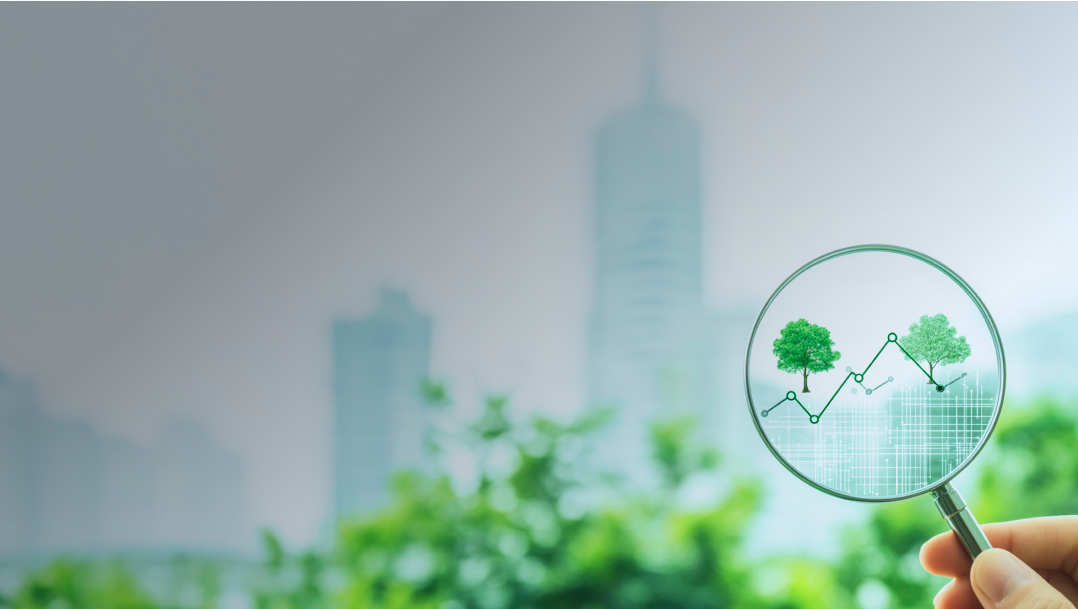
of suppliers passed a sustainability risk assessment
Management Approach
- Set a sustainable procurement policy and guidelines, and a “Supplier Code of Conduct and Guidelines” to inform suppliers about of the guidelines for conducting business together throughout the supply chain.
- Develop criteria for selecting new suppliers and guidelines for dealing with existing suppliers, as well as arrange an annual supplier assessment plan, including an assessment of suppliers’ sustainability risks (ESG Risks) to set standards for jointly conducting sustainable business.
- Set a credit term payment policy to ensure accuracy, transparency and fairness in business operations between suppliers and the Company.
- Support the development of supplier’s potential so that the Company and the suppliers can grow their business together in the long term.
Implementation and Performance
The Company realizes the importance of creating shared value as a fundamental principle for business operation so it is committed to improving the quality of life of all stakeholders to lead to a better future. Therefore, the Company has set strategies to drive the business on the basis of sustainability in the efficient sustainable supply chain management, covering the process of selecting critical tier-1 suppliers including the assessment of risks from the suppliers’ business operations and promoting the suppliers to operate with consideration of the impacts on the environment, society and good corporate governance according to the business ethics of the suppliers. There is an annual supplier assessment to develop and monitor the operations of the suppliers to comply with the supplier guidelines under the business ethics, covering the ESG risk screening of the critical suppliers, supplier selection and registration process, and supplier ESG risk management for supplier identification to ensure that all suppliers of the Company have the potential and can deliver materials, raw materials, products and services with quality that meet the specified standards.
The Company realizes fairness of the procurement system. Therefore, it has set the procurement guidelines, scope of authority to approve, cancel, and amend purchase orders according to the specified process and responsible persons in accordance with the Company's procurement policy that is committed to conducting business sustainably with focus on the principles of good corporate governance, and responsibility for society and the environment. The Company has set the criteria for recruiting/selecting potential business partners who comply with relevant laws and regulations, emphasizing procurement that is fair to all parties without discrimination. The Company also has a standardized internal audit system that is ready to respond to the ever-changing needs and expectations of customers, communities, and society without conducting transactions with individuals or juristic persons who commit illegal or corrupt matters or have behaviors that suggest corruption.
The Company has enhanced the sustainable supply chain management strategies to be in line with the corporate vision of being a leader in the quality and innovative beverage business that grows along with a good society. Therefore, the sustainable supply chain management strategies have been set in 4 main areas:
strategy for selecting and evaluating suppliers with potential to conduct sustainable business
strategy for assessing risks and grouping suppliers
strategy for developing and enhancing suppliers’ potential to be sustainable
strategy for creating awareness, knowledge, and capabilities of employees
to enhance the organization’s competitiveness and promote suppliers’ potential and efficiency to grow together with the organization sustainably.
The Company has integrated sustainability issues into the procurement process under the framework of responsible supply chain management, while promoting suppliers to comply with the Company’s Supplier Code of Conduct, focusing on having positive attitude and cooperating with partners in the supply chain to promote good practice in terms of environment, society and corporate governance. The procurement with responsibility policy focuses on dimensions to achieve and maintain the fundamental principles, as foundation and vision that recognizes the commitment to responsible business, by working with suppliers who comply with the principles within the business according to the business code of conduct which covers the policy on procurement of materials, raw materials, machinery, equipment and chemicals, both domestically and internationally.
The responsible sourcing policy of the Company examines compliance and implementation of necessary requirements specified in the supplier assessment questionnaire to obtain suppliers who meet the following principles in the policy:
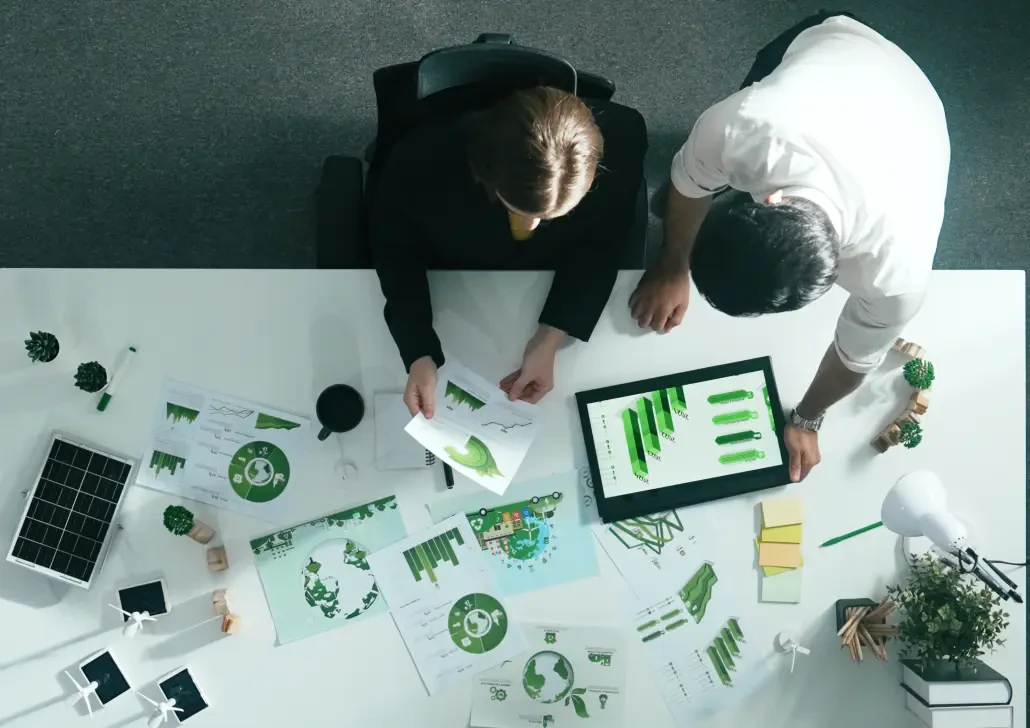
- Suppliers conduct business with honesty, integrity and transparency.
- Suppliers procure safe, quality and eco-friendly raw materials, such as reducing the use of chemicals, pesticides and insecticides in agricultural raw materials, etc., with a system for assessing the authenticity of raw materials.
- Suppliers conduct business under rules, laws and anti-corruption.
- Suppliers procure raw materials under a traceability process. Suppliers must have a system for verifying product codes, batch numbers of materials and raw materials, and be ready to provide information to the Company, including the origin or source of various components in those materials and raw materials for identification and traceability.
- Suppliers comply with national and local environmental regulations and laws.
- Suppliers conduct business in accordance with international labor and human rights laws and principles.
- Suppliers conduct business in accordance with relevant laws and regulation in terms of occupational health, safety and work environment.
- Suppliers conduct business under environmental management in terms of efficient use of water resources, production processes that reduce environmental impacts, waste disposal in accordance with the law without causing troubles in the community, and enhancement of awareness, responsibility, and economical use of resources.
- Suppliers conduct business with consideration for duties and responsibilities towards community and society. Suppliers conduct business in conjunction with environmental care, and do not conduct business that causes social deterioration.
The Company has a policy and goal to treat its business partners with equality and take into account on mutual benefits. Therefore, it has prepared and published the “Business Code of Conduct” covering issues of human rights, labor, environment, and anti-corruption in compliance with standards on safety and occupational health, eco-friendliness, product safety and quality, and traceability. The Company treats its business partners on the basis of fair competition, equality, and mutual respect. It also monitors compliance with the Business Code of Conduct through the Supplier Self-Assessment Questionnaire (SAQ) of key business partners to conduct sustainable business in accordance with the guidelines in this Code of Conduct.
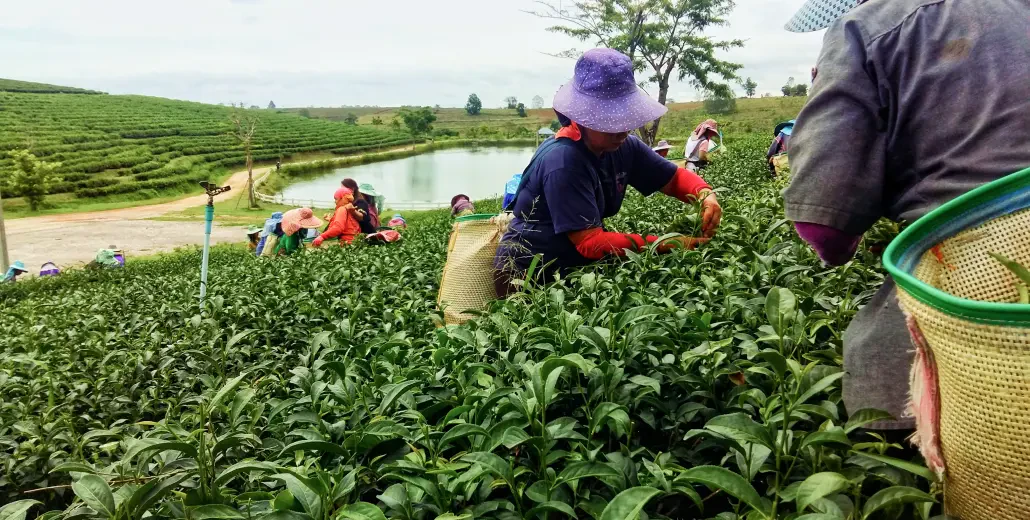
Business Partner Ethics
- Business operation: Business is operated with honesty, transparency, and strict compliance to policies, regulations, rules, morality, ethics, and corporate values.
- Product safety and quality: Business partners must provide quality, safe, and eco-friendly products, have a system for inspecting and assessing authenticity of such raw materials, and disclose true information about possibility of counterfeit and substitution according to economic and trading conditions at that time. The quality of the products must comply with standards and laws of each country in which the company operates.
- Anti-corruption: Business partners of the Company must comply with relevant rules and laws, and must not offer, promise, or give any bribes, gifts, rewards, or benefits to government agencies, customers, or any other persons in order to gain a business advantage. There must be a communication channel for whistleblowers to report suspicious information with confidence that the whistleblower will be protected.
- Traceability: Business partners must have a system for verifying product codes, batch numbers of materials and raw materials, and be ready to provide information to the Company, including the origin or source of various components in such materials and raw materials for identification and traceability.
- Compliance with environmental laws and standards: Business partners must comply with national and local regulations and laws, and support eco-friendly operations.
Child Labor and Human Right Practice
- Prevention of child labor, forced labor and labor oppression: Business partners must fully comply with international labor laws and principles without performing any acts or supporting activities that violate human rights. They must not employ child laborers under the age of 15, and must ensure that workers do not work in areas that are hazardous to their health. They must provide communication channels so that employees can file complaints with the company, and complaints must be treated fairly.
- Employment, compensation and benefits: Business partners must pay regular wages and overtime wages, and normal working hours must not exceed those stipulated by law. They must enter the social security system or other requirements that the Company notifies them to comply with. In the case of using foreign labor, a contract must be drawn up for all workers. The contract must comply with the law and with terms and conditions of employment. The contract must be in a language that workers understand.
Safety and Occupational Health
- Safety and working environment: Business partners must conduct business in accordance with laws and policies on safety, occupational health and working environment with consideration on work safety and hygiene. They must have systems, regulations, practices, and work procedures, and provide safety tools and equipment to employees to prevent accidents from work. They must prepare for emergency situations by organizing drills and continuously improving emergency plans and access to medical treatment in emergency cases.
Environment
- Environmental management: Business partners should operate business with care for environment, comply with environmental laws, manage water resources and waste effectively, do not release chemicals and other hazardous materials that cause troubles to the community, must manage according to the law, create awareness, be responsible, use resources economically, have treatment and restoration measures, and prevent impacts on natural resources and environment sustainably.
Society
- Business partners should conduct business with due regard to their duties and responsibilities towards the community and society, conduct business alongside caring for environment, not conduct business that causes social deterioration, and not violate the rights of other people living in the community and society, such as stopping deforestation, reducing greenhouse gas emissions and waste, and using resources efficiently.
In selecting local suppliers, the Company conducts a preliminary supplier assessment by examining a checklist according to the form specified by the Company, such as raw materials sold to the Company, suppliers’ production processes, quality assurance, good characteristics and cleanliness of the raw materials, contamination and genetic modification, environmental and social operations, etc.
After the suppliers have conducted a preliminary self-assessment, the Company conducts an assessment of the suppliers’ operations before ordering to ensure that the suppliers comply with the agreement and standards as specified.
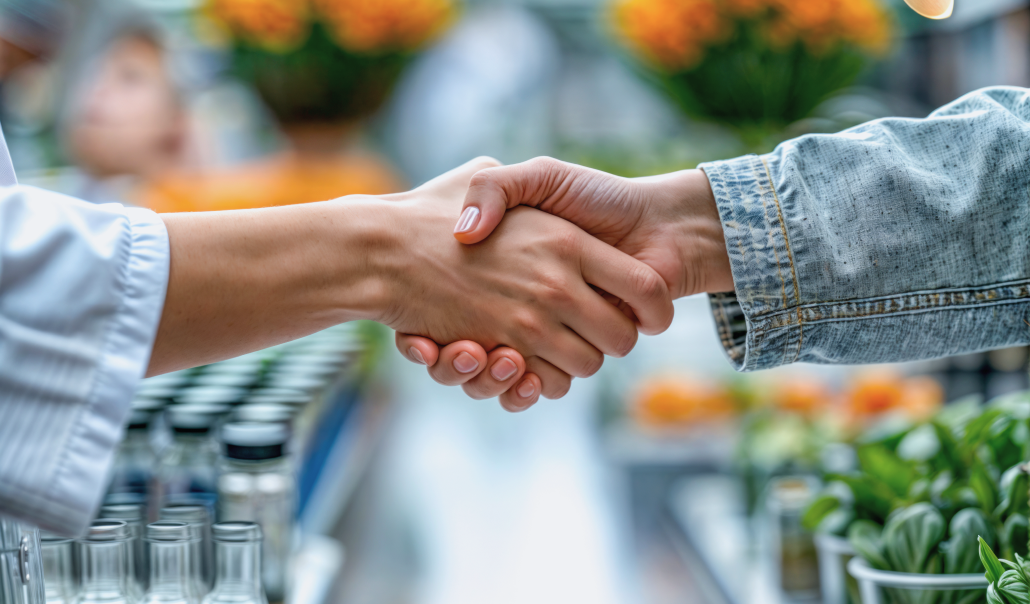
The Company places importance on managing the cash flow cycle in order to maintain business liquidity in the long term, as well as taking into account equality in doing business with suppliers by emphasizing on building good relationships and cooperation, adhering to the contract, and complying with conditions fairly made with suppliers, setting appropriate payment terms, and making payment on time in accordance with the business terms agreed upon. The Company has set the Credit Term Policy for suppliers to ensure correctness, transparency and fairness in doing business between supplers and the Company.
The Company has a policy to set credit term to its suppliers between 30 and 60 days (average 45 days). Such term may vary, and is subject to mutual agreement or negotiation between the Company and each supplier, along with the nature of the suppliers’ operations, the period of time the Company and the suppliers have been conducting business together, and other factors considered appropriately to maximize the Company's efficiency. In the event that the Company is unable to comply with such terms and conditions, the Company will directly clarify to the suppliers in advance.
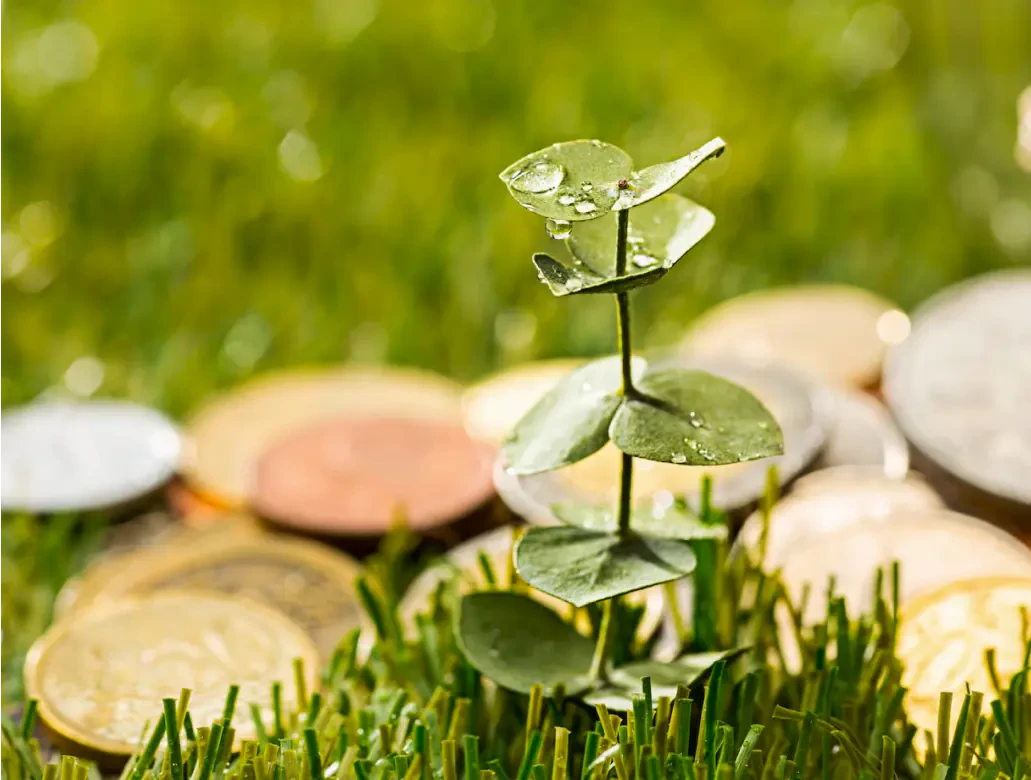
Performance
(Unit: m3)
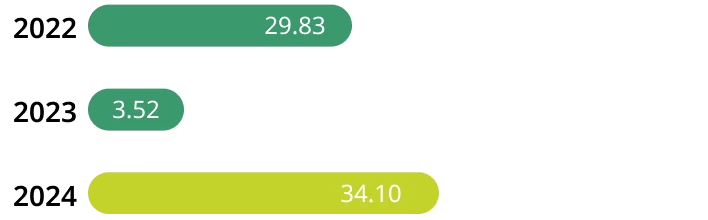
Over the past 3 years, the Company has never had a history of defaulting on any debt with any suppliers, as detailed below:
(Unit: days)
Performance | 2022 | 2023 | 2024 |
---|---|---|---|
Average payment period to suppliers | 29.83 | 3.52 | 34.10 |
In order to effectively manage critical suppliers, in 2024, the Company assessed the risks of critical suppliers, covering ESG Risks and grouping them according to the risk and severity levels of the impacts. The Company focuses on managing critical suppliers in the supply chain with high risk levels or severe impacts first. In the assessment, 100% of all suppliers in the main supply chain responded the Self-Assessment Questionnaire (SAQ). Critical suppliers were divided into 2 main groups according to product types: raw materials and packaging. From the self-assessment of the suppliers, all suppliers in the supply chain passed the Self-Assessment Questionnaire (SAQ).
Number of Suppliers Passing the Assessment
80 suppliers
Self-Assessment Questionnaire 79 suppliers
On-Site Audit 1 supplier
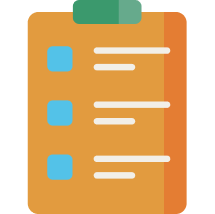
Raw materials
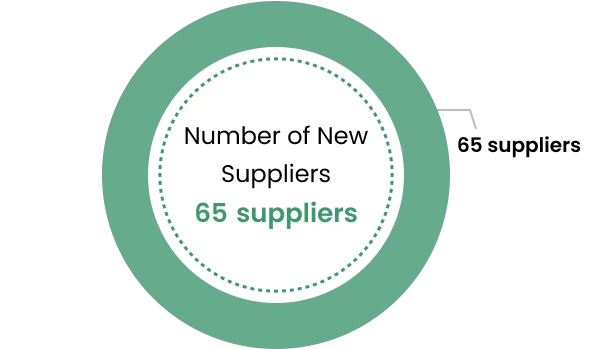
Packaging
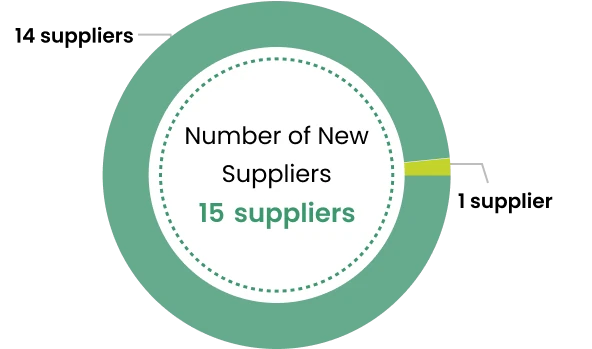
Product Types of Suppliers | Number of New Suppliers | Number of Suppliers Passing the Assessment | |
---|---|---|---|
Self-Assessment Questionnaire | On-Site Audit | ||
Raw materials | 65 | 65 | - |
Packaging | 15 | 14 | 1 |
Total | 80 | 79 | 1 |
In 2024, 80 new suppliers passed the Supplier Self-Assessment Questionnaire (SAQ) in accordance with the 100% vendor monitoring plan. On-site audit was performed with 1 supplier in the packaging product category to ensure that the products meet the standards of the specified assessment criteria. In addition, the Procurement Department reviews the supplier selection assessment form every year to cover more in-depth details of ESG risk issues.
The Company manages sourcing risk and geopolitical risk by continuously expanding the approved supplier list in the supply chain, both domestically and internationally, to be distributed in each region to reduce the risk if suppliers are unable to deliver raw materials to the Company.
In 2024, the Company procured from domestic suppliers, accounting for 98.75% of all purchases in the supply chain, and procured from international suppliers, accounting for 1.25%, to reduce the impact of economic, social and political volatility, as well as other external factors such as natural disasters that occur in the areas where suppliers operate business. In addition, the Company also considers industry context risk that is a risk arising from the specific characteristics of the industry in which the suppliers operate, and product context risk that is a risk from products that partners manufacture or have for sale, etc.
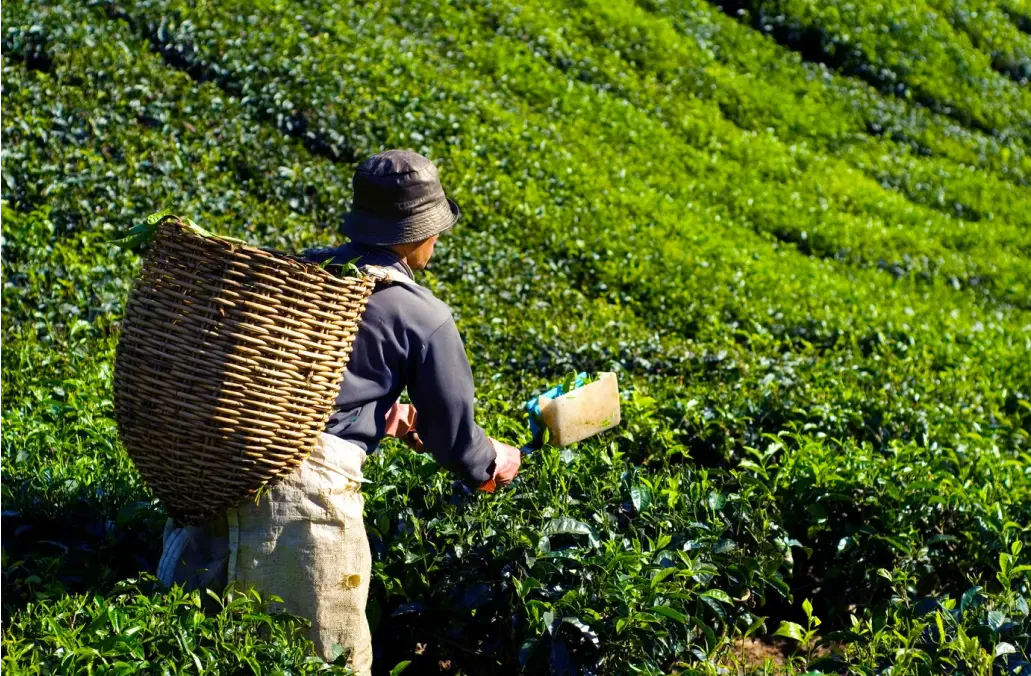
The Company places importance on supplier development. Therefore, it promotes, supports and cooperates with suppliers to develop their capabilities and work efficiency to be better and in accordance with the Company's standards. This will enable the Company to reduce business risks and develop supplier potential to grow together in the long term by focusing on developing production processes, promotion, and providing advice on upgrading quality management systems and safety and environmental systems of the suppliers. In addition, this implementation can enhance a long-term relationship by linking and building good relationships with suppliers.
In 2024, the Company implemented an rPET packaging development project with a partner, Envicco Co., Ltd., by collecting 639,936 plastic bottle waste from the Ichitan factory and nearby communities through a plastic bottle waste buyer, totaling 311,200 kilograms of plastic, to the Envicco factory in Rayong Province to produce recycled plastic pellets, and send them back to Hon Chuan (Thailand) Co., Ltd. to produce rPET Resin into rPET Preforms for delivering to Ichitan to re-form product bottles.
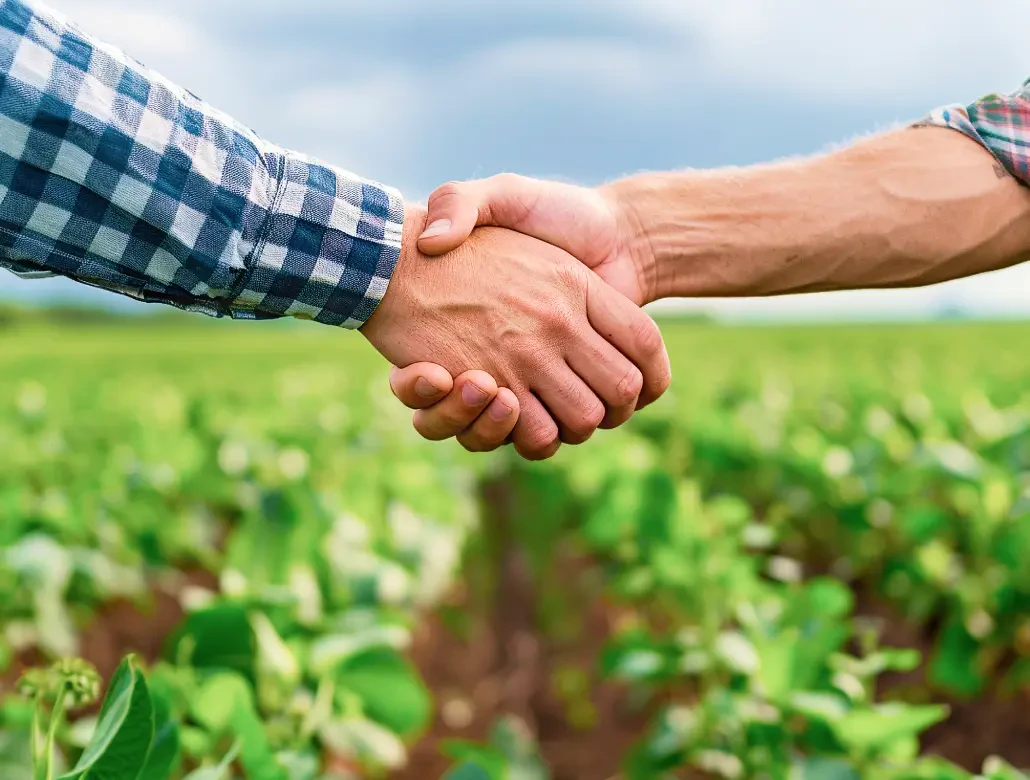
In addition, the Company has changed to use perforated labels for Ichitan Green Tea 500 ml., Shizuoka 440 ml. and Ichitan Alkaline Water 550 ml. products, in collaboration with several leading label-selling suppliers, including Fuji Seal Packaging (Thailand) Co., Ltd., Shringflex (Thailand) Public Company Limited, and CCLA Label (Thailand) Co., Ltd., etc., to help consumers easily remove labels from bottles, allowing the packaging to enter the recycling process.
Note: The project performance is disclosed in the Sustainability Issue under the Environment topic for the year 2024
The context of business operations in the present era requires adjustment to be in line with economic, social and environmental conditions throughout the supply chain so that the companies can operate their business under the constant changes at both the national and international levels, whether it is food security, traceability of raw materials, production processes that reduce impact of climate change, and increasingly stringent food business safety.
Therefore, the Company focuses on collaborative management with partners and relevant sectors throughout the supply chain, and aims to encourage partners to participate in preventing impacts that may affect the shared value among the companies, along with caring for environment and developing communities that are important locations. The Company is committed to developing criteria for selecting partners to demonstrate responsible business operations, creating competitiveness together with partners throughout the supply chain for continued mutual sustainability.
Criteria for Supplier Selection
The Company has a process for selecting suppliers by having them compete on equal information and selecting partners fairly under the Company's criteria for evaluating and selecting suppliers. In addition, the Company has prepared contract forms that are appropriate and fair to all contracting parties, and has a monitoring system to ensure that the terms of the contract are fully complied with, and to prevent corruption and misconduct at every step of the procurement process. The Company purchases products from suppliers according to trade terms and strictly complies with contracts with suppliers, and keeps their information without using it for improper purposes.
Selection of New Suppliers
The Company continuously manages its supply chain responsibly and efficiently, and integrates sustainability issues into the recruitment and selection of new suppliers at every stage. The Company communicates its policies and expectations to suppliers, and sets criteria for assessing potential and qualifications for new supplier selection, covering main social and environmental issues as follows:
- Product quality and safety
- Appropriate capability in production and cost management
- Appropriate capability in delivery and services under relevant regulations and laws
- Capability in sustainability implementation
Criteria for Assessing Potential and Qualifications for Selecting New Suppliers, Covering Key Issues
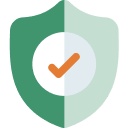
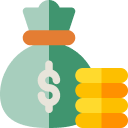
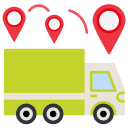
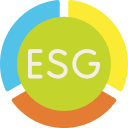
The Company considers the results of the supplier selection with sustainability criteria set by the Company. If any supplier does not pass the minimum score from the supplier selection with sustainability criteria within the specified time frame, the contract will not be considered for renewal to ensure that the suppliers’ operations comply with the law and various practices in order to reduce potential risks.
In addition, the Company has set supplier risk screening, covering all Tier-1 Suppliers, both existing suppliers and new suppliers, under responsibility of the Procurement Department and Risk Management Department to continuously search for initial risks of suppliers by using the Risk-based Due Diligence tool.
Dealing with Current Suppliers
The Company has criteria for considering and evaluating current suppliers by basing on product quality and safety, price, performance, and ESG assessments. The consideration process is as follows:
- Suppliers conduct annual quality assessments whereby the Quality Assurance Department reviews and summarizes the results of the quality inspection records, product information, characteristics, transportation conditions, remaining shelf life of raw materials and packaging according to the specified standards before being produced as products, and annual ESG assessment.
- Selection criteria for suppliers must undergo annual on-site audits whereby the Quality Assurance Division stipulates that the vendors must be randomly audited at least once a year according to the specified plan.
The Company's suppliers, vendors, or business partners mean those who produce raw materials, sell products, are hired, and/or provide services to the Company, whether they are juristic persons or ordinary persons, and are not “customers or business competitors.”
Criteria for Identifying Critical Suppliers
- High-volume suppliers
- Critical component suppliers, which have significant impact on competitive advantage and market success
- Non-substitutable suppliers, such as suppliers of materials/raw materials with special orders that meet the company's requirements
Criteria for Identifying Critical Tier 1 Suppliers
The consideration is based on the value of purchase orders for materials/raw materials in the past year, as follows:
- Critical suppliers are suppliers in the material/raw material category with a total purchase value and sales value exceeding 30 million baht.
- Non-critical suppliers are suppliers in the material/raw material category with a total purchase value and sales value less than 30 million baht.
Criteria for Considering Critical Non-Tier 1 Suppliers
Critical non-tier 1 suppliers refer to suppliers of raw materials, products and services to the Company's Tier 1 Suppliers, whose raw materials, products and services have significant impact on the Company's competitive advantage, market success or survival, and they are few in number or cannot be replaced.
In 2024, there were 80 new suppliers, 79 domestic suppliers, accounting for 98.75% of all suppliers, and 1 international supplier, accounting for 1.25% of all suppliers, all of whom passed the Supplier Self-Assessment Questionnaire (SAQ).
Criteria for Supplier Assessment
The Company plans an annual supplier audit by delivering Vendor Visit Check Sheet / Supplier Self Audit documents, and conducting an on-site audit. The consideration of which supplier to be audited will be based on the following criteria:
- New vendors who have not yet conducted an audit or self-audit.
- Vendors who frequently encounter problems about product quality or encounter significant quality problems that may affect product quality.
- Vendors who have changed production locations or production processes.
- Existing vendors who supply the Company with main raw materials, or the Company has ordered in large quantities, and has not been audited for more than 2 years.
- Vendors of materials/raw materials that the Company's customers are particularly strict about, or changes in food laws requires strictness. For vendors who do not meet these criteria, the Company will deliver Vendor Visit Check Sheet / Supplier Self Audit documents for the suppliers and/or vendors to fill in the details.
In 2024, 100 percent of all new Tier 1 suppliers and non-Tier 1 suppliers of the Company have passed the sustainability risk assessment as specified by the Company. The Company uses the ESG Supplier Assessment Criteria as part of the supplier selection to work with the Company, and applies the ISO 14001 Environmental Standard as the criteria for supplier assessment in terms of pollution management system assessment, wastewater treatment and wastewater quality inspection, toxic fumes control system, natural resource management system, etc. Regarding the criteria for assessing social suppliers, the Company has applied the principles of business ethics and human rights management, use of foreign labor and child labor, assessment and inspection of work safety systems, supervision of good corporate governance, and anti-corruption. The Company has conducted an assessment of the operations of new suppliers before placing orders, and has continuously inspected and monitored the results to ensure that suppliers comply with the agreements and standards as specified, as well as to ensure that suppliers who will join the Company's business are concerned with operations that are socially and environmentally friendly.
Green Procurement Process
The Company has established green procurement practices as part of the procurement process with the following implementation:
- Increase the number of suppliers and the lists of eco-friendly materials/raw materials.
- Continuously communicate the green procurement guidelines to stakeholders.
Guidelines for Promoting Supplier Potentials and Capabilities
The Company has policies and processes for promoting supplier potentials and capabilities by cooperating in developing products and innovations that are beneficial to the Company's and its suppliers’ businesses. The Company is also committed to participating in improving the quality of life of farmers, who are a part of the Company's partners, so that they have a good life and are supported in creating careers and incomes. The Company aims to develop the farmers’ quality of life to grow along with the Company. In 2024, the Company promoted farmers to have incomes worth 709.6 million baht, or 18.5 percent of the total budget for purchasing raw materials, to be used in purchasing main raw materials from farmers and middlemen, such as tea leaves, sugar, etc.
2024
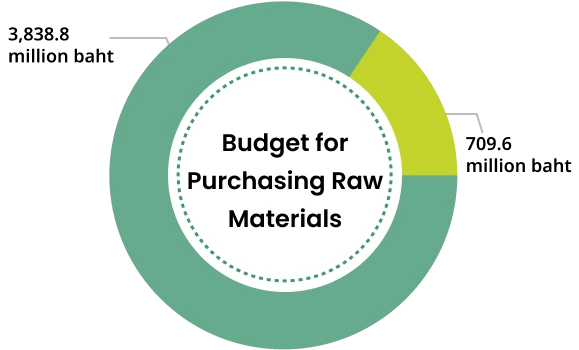
2023
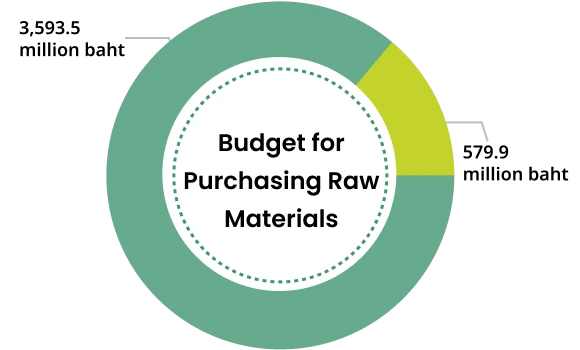
2022

Year | Budget for Purchasing Raw Materials | |
---|---|---|
All Suppliers | Local Suppliers | |
2022 | 3,076.5 million baht | 494.1 million baht |
2023 | 3,593.5 million baht | 579.9 million baht |
2024 | 3,838.8 million baht | 709.6 million baht |